During the past months, DLR, Tecnalia, Ghent University and ECT tested and improved all their respective individual technologies. Based on the results, the researchers carried out additional tests and modification to improve the performance before all components are assembled in the overall CHEST technology. What optimizations and test have been made so far?
Power cycle prototype, Ghent University
The Ghent University (Ghent, Belgium) has now finalized the building and the testing campaign of the Power cycle prototype (ORC). Currently, DLR (Stuttgart, Germany) is expecting to integrate the ORC in its laboratories.
All connections will be checked, and all functionalities will be tested separately before the operation with the latent heat storage system as an evaporator for the ORC is carried out. The integration of the ORC with the rest of the CHEST components will be done in the upcoming months.
For the last 6-months, the team in Ghent University has been analyzing the experimental results obtained during testing campaign of the Power cycle prototype (ORC). The researchers carried out in depth analyses to make modifications of the ORC in order to improve its operation.
During this time, the team also fine-tuned the simulation model that is used for designing the ORC prototype. In addition, they also validated it with the experimental data to predict the electrical output of the prototype. Therefore, this is now possible with an average relative accuracy of only 3.1 %. Furthermore, the model is also used to generate a performance map to estimate the output of an upscaled CHEST system.
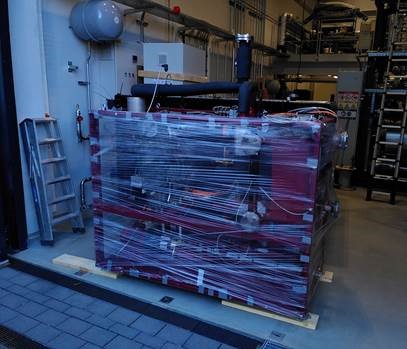
High temperature thermal energy storage HT-TES, DLR
For past months, DLR (Stuttgart, Germany) has prepared the test setup and filled the latent heat thermal energy storage unit (LH-TES) with the phase change material (PCM). The PCM is a eutectic mixture of potassium nitrate and lithium nitrate.
The filling process consists of several consecutive and iterative steps in which the two substances are mixed and then filled into LH-TES unit from the top. Thereby, the nitrate salts are in powder condition. Then the PCM is melted and actively solidified again. Since the volume reduces after melting, the filling process must be repeated until the required quantity is reached. Currently, the storage prototype is being characterized following a previously defined test matrix.
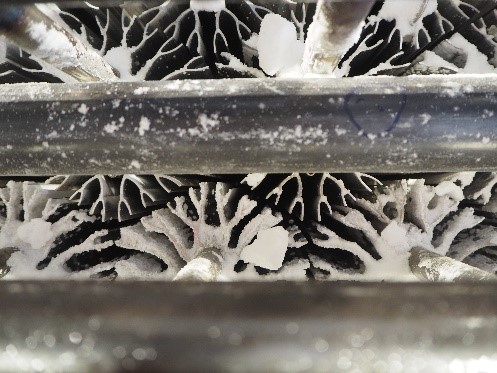
The Isobaric expansion (IE) engine pump, ECT
ECT has carried out couple of modifications in the Isobaric expansion (IE) engine pump to improve its performance. Originally, it was expected that the engine would operate effectively at the heat source temperatures above 80°C. However, it turned out that the engine can operate even at much lower temperatures.
Therefore, the team has studied the performance of the newly developed IE engine at ultra-low heat source temperatures of down to 30°C. That was done by using tap water with temperature of 15°C as a heat sink.
It was found that the engine showed excellent performance at the very low temperature differences of 20-30°C. In particular, relative to the Carnot efficiency at the heat source temperature of 60°C is about 35% and above 40% at 40°C. The ability to use such low temperature differences significantly expands the capabilities of IE technology.
In addition, engine-pump was modified to generate shaft power (rotary motion) and then electricity and/or drive any rotating equipment such as centrifugal pumps, compressors etc.
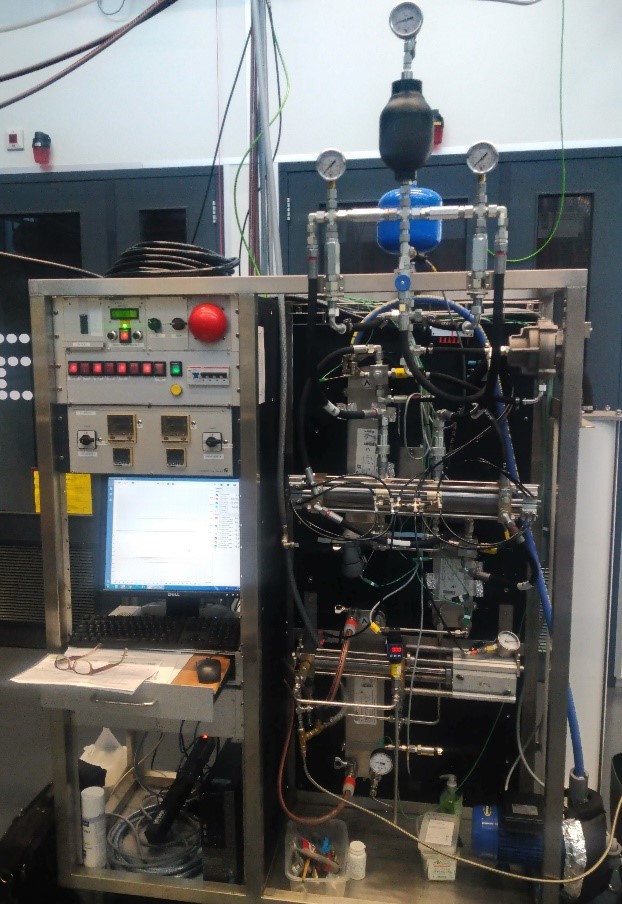
Furthermore, ECT has designed a new high-pressure hydraulic circuit. It was built to operate with hydraulic oil instead of water. The energy of the pumped oil is converted to shaft power by a hydraulic motor. The use of the oil permits to apply a wider range of commercially available hydraulic motors.
The available hydraulic motor requires a rather high pressure drop of about 80 bar for the most efficient operation (overall efficiency up to 96 %). Therefore, the generated pressure was increased to 80 bar. This was done by using a differential piston pressure transformer instead of the water pumping unit.
Thus, the installation can be turned into a heat-driven electric generator. In contrast to the conventional well-known generators, it can also produce electricity using very low-grade heat (> 30 °C) available in the CHEST system. This development will significantly expand the capabilities within the CHEST system.
READ MORE
High temperature heat pump (HTHP) prototype, Tecnalia
Tecnalia (San Sebastian, Spain) carried out additional tests under specific conditions to evaluate and optimize the control algorithm. The researchers focused their main work on operating modes during charging of the LH-TES and the safety features. They tested the prototype using a common plate heat exchanger for a condenser instead of a phase change material.
Thus, Tecnalia implemented a control strategy to operate in transient capacity conditions when integrated into the CHEST system. Therefore, the control loops of the compressor motor speed, the water pumps and the expansion device were programmed to deal with the load variations while maintaining the optimum efficiency of the system.
Tecnalia further optimized the compressor´s lubrication and cooling loops, the structural robustness of both components, as well as the prototype itself. Moreover, the research team also made improvements in the connections required for the integration of the prototype in the CHEST system.
In addition, all required certifications and requirements to guarantee equipment and personal safety during all operation were met. An independent third-party inspected the HTHP to verify and approve the conduction of safe operations.
As a conclusion, Tecnalia carried out all the tasks related to the disconnection and preparation of the prototype before shipping it to DLR. Currently, the HTHP prototype has been sent in DLR´s facilities in Germany and is ready for integration with the rest of the CHEST system components.
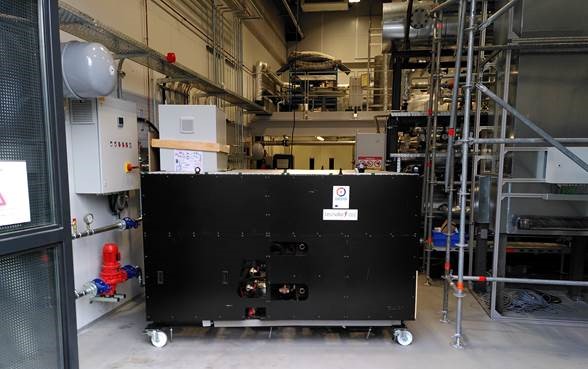